What is 5356 aluminum wire used for?
5356 aluminium alloy is an alloy in the wrought aluminium-magnesium family (5000 or 5xxx series). Unlike most aluminium-magnesium alloys, it is primarily used as welding filler. It is one of the most popular aluminium filler alloys, alongside 4043.
What is 4043 aluminum used for?
4043 aluminium alloy is a wrought aluminium alloy with good corrosion resistance typically used as filler material for welding of aluminium parts. It contains high amounts of silicon (between 4.5 and 6%) and trace amounts of other metals.
When to use 5356?
A 5356 aluminum filler metal would be most appropriate for: Welding on 5XXX or 6XXX series of aluminum when tensile strength is most important. Achieving good anodized color matching on 5XXX and 6XXX base metals. Applications requiring higher ductility and toughness (such as those subject to dynamic loading).
What is the best wire for aluminum welding?
ER4043 is often used in applications where aesthetics are critical, such as automotive and architectural projects. ER5356 is another commonly used aluminum welding wire for MIG welding. This wire is particularly suitable for applications requiring high tensile strength and good corrosion resistance.
Which is stronger, 4043 or 5356?
Shear Strength – 4043 has lower shear strength than that of 5356 (see Fig 1). This may be of consideration when calculating the size of fillet welds.
What is the difference between ER5356 and ER4043 welding wire?
ER4043 can be used in working environments with operating temperatures exceeding 150°F (66°C). In contrast, ER5356 filler metal is not suitable for prolonged high temperature environments due to its 5% magnesium content.
What can I weld with 4043 wire?
For 6xxx series base metals, and 5xxx series base metals containing up to 2.5% (nominal) Magnesium use either 4043/4943 or 5356. For 5xxx series base metals containing more than 2.5% (nominal) Magnesium use 5356 filler metal and do not use 4043/4943 filler metal.
Can you weld 6061 aluminum with 5356 wire?
Selecting a suitable filler metal for 6061-T6 welding requires careful consideration of two primary options, 4043 and 5356, each offering distinct advantages and varying degrees of crack resistance.
Can you weld 5052 aluminum with 4043 wire?
However, the magnesium content of 5052 is low enough that 4043 works just fine.
Can you weld cast aluminum with 5356?
Fortunately, both the 3XX and 5XX casting alloys are readily weldable. Make sure to weld 3XX alloys with 4043 filler, and 5XX alloys with 5356 filler. Roughly 80% to 90% of the castings you will ever encounter are 3XX, such as 357, 319, and the most common, 356.
What is the strength of 4043 weld filler?
4043 Aluminum MIG Wire, TIG Rod & Brazing Alloys F with a density of . 097 lbs./cu.in. The average tensile strength is 27,000 psi, average yield strength of 18,000 psi and the post anodizing color is gray. 4043 aluminum filler metal is one of the oldest and most widely used welding and brazing alloys.
What is ER5356 used for?
ER5356 materials are used mainly for welding aluminum of like composition. This type is also useful if color match is important after anodizing.
What is 4043 welding rod used for?
4043 is an all-position 5% silicon alloy used to weld heat treatable base alloys. It is most often used to weld the 6XXX series of alloys. The silicon addition improves puddle fluidity, producing an appealing bead profile.
What is best for welding aluminum?
Gas Tungsten Arc Welding (GTAW)/ TIG This is the most common method of welding aluminium. It is also known as Tungsten Inert Gas welding. This method doesn’t require mechanical wire feeding, which saves you the problems that come with feedability issues.
Do you need different wire to weld aluminum?
Are there any general-purpose aluminum welding wires? Traditionally, welders have relied on AWS 4043 and 5356 wires, as they can be used with the most widely used aluminum alloy base metals. Hobart, however, offers an alternative to 4043 filler metals to increase strength and quality.
What is 5356 aluminum used for?
Aluminum 5356 alloy is used for filler wires and electrodes in the welding process of aluminum alloys with high-magnesium content.
What is aluminum 4043 equivalent to?
Equivalent materials to the aluminium / aluminum 4043 alloy are listed below: BS N21. MIL-W-6712. Alcan GB-33S.
Can 5356 aluminum be anodized?
But if the component will be anodized after welding, use 5356. The high silicon content of 4043 will cause the weld to turn black during anodizing, making the location of each weld obvious and unattractive; 5356 will anodize to a silver color.
What is the difference between 4043 and 5356 TIG rod?
Briefly, 4043 is easier to weld with and provides a better appearance. 5356 is stronger, which is not really important for groove welds. However, the picture changes a bit if you are assembling a structure using fillet or lap welds.
What is the most common aluminum welding wire?
Even though there are various grades of aluminum, as a hobbyist, you are likely to use ER4043 or ER5356 wires. These are both general-type, all-position welding wires that provide good results and desirable weld properties on a wide variety of aluminum alloys, and the choice will differ on specific applications.
Can you weld 6061 with 4043?
While the 4043 filler alloy, a 5% Silicon alloy, is often used to weld 6061 base materials, it is not commonly used when the shear strength of the component is a predominant consideration.
What is ER 4043 used for?
DESCRIPTION: Pinnacle Alloys ER4043 is a 5% silicon, all position aluminum weld wire used to weld heat treatable alloys such as the 6XXX base metals and cast alloys. It can be found in many common welding applications, such as bicycles, trucks, trailers, and automotive parts and equipment.
Can you weld 6061 with 5356?
Filler 5356 has other benefits that make it valuable for welding 6061. The other main benefit of 4043 is that it produces a very bright finish and a lot less sooting, which is the black lines you might see on the edge of a 5356 weld.
What is the tensile strength of 5356 aluminum?
Average tensile strength as welded is 28,000 psi.
What is the best wire for welding cast aluminum?
Aluminum Wire This is the most common type of wire used in aluminum welding, as it is specifically designed for use with aluminum. Aluminum wire is made from pure aluminum and is available in a variety of sizes and alloys. One of the best things about aluminum wire is that it makes a strong bond that doesn’t rust.
What is ER5356 wire used for?
ER5356 materials are used mainly for welding aluminum of like composition. This type is also useful if color match is important after anodizing.
Can you weld cast aluminum with 5356?
Fortunately, both the 3XX and 5XX casting alloys are readily weldable. Make sure to weld 3XX alloys with 4043 filler, and 5XX alloys with 5356 filler. Roughly 80% to 90% of the castings you will ever encounter are 3XX, such as 357, 319, and the most common, 356.
What is the tensile strength of 5356 aluminum?
Average tensile strength as welded is 28,000 psi.
What is aluminum wire used for?
Aluminum provides a better conductivity-to-weight ratio than copper, and therefore is also used for wiring power grids, including overhead power transmission lines and local power distribution lines, as well as for power wiring of some airplanes.
What are 4043 and 5356 alloys?
What is welding wire 4043 used for?
Which filler wire is best for welding 6061-T6 aluminum?
Should a weld be 5356 or 4043?
The Lowdown on 4043 and 5356
First things first, both 4043 and 5356 are aluminum-silicon alloys. That means they’re primarily aluminum, but they have a bit of silicon mixed in, which is like adding a secret ingredient to give them special powers.
4043
4043 is like the “all-rounder” of aluminum welding wire. It’s got a great balance of strength, corrosion resistance, and weldability. Think of it as the friendly neighbor you can always rely on. This wire is super versatile and used for a ton of different applications.
5356
5356 is known for being tougher and more resistant to cracking. This is because it has a higher silicon content than 4043. Imagine it as the strong, silent type – it might not be as flashy, but it’s got serious staying power. It’s often used in situations where you need welds to hold up under a lot of stress.
What’s the Difference?
The main difference between these two is their silicon content. 4043 is typically around 5% silicon, while 5356 can have as much as 10%. That higher silicon content in 5356 makes it better for welding thicker aluminum, especially in applications where there’s a lot of stress or vibration.
Picking the Right Wire for the Job
So, how do you know which one to use?
If you’re welding thin aluminum, 4043 is probably your best bet. It’s easier to control and gives you a smoother weld bead.
If you’re welding thick aluminum or working with something that needs to be really strong, 5356 is your go-to.
But remember, there’s more to it than just the thickness of the aluminum. You also need to think about:
The type of aluminum you’re welding (some types are more prone to cracking)
The environment the weld will be exposed to (corrosion, heat, etc.)
The desired weld strength
Important Points to Keep in Mind
Here are a few things to remember when using 4043 or 5356:
Cleanliness is key. Aluminum is a finicky metal. Make sure your workpiece and welding wire are clean and free of any oils, grease, or other contaminants. Otherwise, you’ll end up with a weak, porous weld.
Preheating is sometimes necessary. If you’re welding thick aluminum, preheating it can help prevent cracking and ensure a good weld.
Choose the right welding process. Both 4043 and 5356 can be used with a few different welding processes, like Gas Metal Arc Welding (GMAW), Gas Tungsten Arc Welding (GTAW), and Flux-Cored Arc Welding (FCAW). The best process will depend on the thickness of the aluminum, the type of application, and your personal preferences.
Proper shielding is essential. You need to shield your weld from the atmosphere to prevent oxidation. This is done with a shielding gas, like argon or helium.
Post-weld cleaning is important. Once you’re done welding, you’ll need to clean the weld area to remove any slag or spatter. This will give you a nice, finished look and help prevent corrosion.
Common Applications
4043 and 5356 are used in a wide range of applications, including:
Automotive – think car bodies, wheels, and engine parts
Aerospace – where lightweight and high strength are crucial
Marine – for boat hulls and other parts exposed to harsh environments
Construction – from aluminum siding to window frames
Manufacturing – a huge variety of products, like appliances and machinery
FAQs
Here are some frequently asked questions about 4043 and 5356 aluminum welding wire:
Q: Can I use 4043 wire on thick aluminum?
A: While you technically can, it’s not ideal. 4043 tends to crack when used on thick aluminum. 5356 is a better choice for thicker materials.
Q: Which wire is better for welding aluminum to steel?
A: You can’t directly weld aluminum to steel using 4043 or 5356. You’ll need to use a special filler metal specifically designed for this purpose.
Q: What is the difference between 4043 and 5356 in terms of strength?
A:5356 is generally stronger than 4043 because of its higher silicon content. This added strength makes it a better choice for applications where high-stress welds are required.
Q: What kind of shielding gas should I use with 4043 and 5356?
A:Argon is the most common shielding gas for welding aluminum with both 4043 and 5356. Helium can also be used, but it’s more expensive and less commonly used.
Q: Can I use 4043 or 5356 for brazing aluminum?
A: No, these wires are designed for welding, not brazing. Brazing uses a different type of filler metal with a lower melting point.
Q: What are the advantages and disadvantages of using 4043 and 5356?
A:
4043:
Advantages: Versatile, easy to use, good for thin aluminum, good corrosion resistance
Disadvantages: Can crack on thicker aluminum, lower strength than 5356
5356:
Advantages: High strength, good for thick aluminum, resistant to cracking
Disadvantages: More difficult to control, more expensive than 4043
Q: Is it possible to weld aluminum to stainless steel?
A: Yes, you can weld aluminum to stainless steel, but it requires special filler metal and a skilled welder to ensure a strong and reliable bond.
Q: What is the typical size of aluminum welding wire?
A: Aluminum welding wire comes in various diameters, but common sizes are .035″, .045″, and 1/16″. The size you need will depend on the thickness of the aluminum you are welding and the welding process you are using.
Q: Can I use 4043 or 5356 on galvanized steel?
A: It’s not recommended to directly weld to galvanized steel with 4043 or 5356. The zinc coating on galvanized steel can create harmful fumes and affect the weld’s quality. It’s best to remove the zinc coating before welding.
Q: How do I store aluminum welding wire properly?
A: Store your aluminum welding wire in a cool, dry place away from direct sunlight and moisture. You should also avoid storing it near corrosive substances.
Q: How do I know if I’m using the right welding wire?
A: Check the wire’s AWS classification or the ER number on the spool. This will tell you exactly what the wire is made of and what it’s intended for.
Conclusion
4043 and 5356 are both excellent choices for aluminum welding, each with its strengths and weaknesses. Knowing which one to use for a specific project is crucial to achieving strong, reliable welds. By understanding the differences between these two wires, you can confidently select the right one for your next welding project.
See more here: What Is 4043 Aluminum Used For? | Aluminum Welding Wire 4043 Or 5356
Aluminum Workshop: Deciding between 4043 and 5356 filler metal
Briefly, 4043 is easier to weld with and provides a better appearance. 5356 is stronger, which is not really important for groove welds. However, the picture changes a bit if you are assembling a structure using fillet or lap welds. The Fabricator
Aluminum welding wire 5356 vs 4043 | Weldermetals
ER4043 and ER5356 are the most commonly used aluminum alloy wire grades, which specified in the requirements of AWS A5.10/AWS A5.10M. Aluminum-magnesium alloy 5356 is a kind of aluminum alloy filler weldermetals.com
Should I use 4043 or 5356 filler alloy? – NORTH AMERICA
Alloy softness – 4043 is a softer alloy in the form of spooled wire when compared to 5356. Typically, when Gas Metal Arc Welding (GMAW), feedability will become a less critical ESAB
4043 v 5356 Aluminum Filler | WELDING ANSWERS
Should I use 4043 or 5356 aluminum wire for my application? This is a very commonly asked question. The application of these two aluminum alloys has such a big overlap that a lot of times it simply comes down to WELDING ANSWERS
Aluminum Workshop: The best filler wire for welding 6061-T6
Q: Which filler wire is best for welding 6061-T6 aluminum, 5356 or 4043? A: Both are acceptable for welding 6061-T6, but each has advantages and disadvantages The Fabricator
Should I Use 4043 or 5356 Filler Alloy? – esab.com
One common misconception is that any aluminum base alloy can be successfully welded with either 4043 or 5356 filler alloy. Which one should you choose? ESAB
Should I Use 4043 or 5356 Filler Alloy? – esab.com
Alloy softness – 4043 is a softer alloy in the form of spooled wire when compared to 5356. Typically, when Gas Metal Arc Welding (GMAW), feedability will become a less critical ESAB
Aluminum Welding Guide – Hobart Brothers
For better feedability through the welding gun use 5356. 5356 is twice as stiff as 4043/4943 and therefore feeds better. However, MAXAL’s 4043/4943 has excellent feedability. Hobart Brothers Filler Metals
Aluminum filler metals: What you should know about
The most common aluminum filler metals are 4043 and 5356 alloys, both of which are available in wires for gas metal arc welding (GMAW) and cut-lengths (often called filler rods) for gas tungsten arc The Fabricator
ER4043 VS ER5356 Aluminum Welding Wire – marine alu
ER4043 and ER5356 aluminum welding wire are two of the most widely used filler metals in the aluminum fabrication industry. What are their differences and application scope? marinealu.com
See more new information: activegaliano.org
4043 Vs 5356 What Aluminum Filler To Use, When And Where
4043 Vs 5356 Filler Rod – Quick Comparison
Aluminim Filler Wire For Repair Work Which Grade To Choose 4043 Vs 6061
Tig Welding Aluminum! 4043 Vs 5356 Comparison!
Tig Welding Aluminum 5356 Vs 4043 Filler Rod
Link to this article: aluminum welding wire 4043 or 5356.
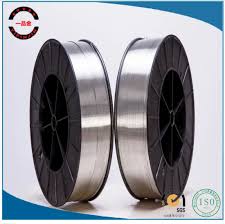
See more articles in the same category here: activegaliano.org/bio